This course is certified by the European society for precision engineering & nanotechnology (euspen) and the Dutch Society for Precision Engineering (DSPE) and leads to the ECP2-certificate.
This course focuses on the various aspects related to thermal effects that impact the performance (accuracy, life time or process quality) of precision modules/systems. Participants will acquire theoretical and practical background on design, simulation, measurement and compensation techniques that are essential in the development of precision modules/systems that are subject to internal or external thermal loads.
This training is available for open enrollment as well as for in-company sessions.
Objective
After completion of the course, the participants understand the basic aspects, risks and concepts related to thermal effects and judge solutions and implications on system level.
Target audience
This course is intended for mechanical designers, mechatronics system engineers and mechatronic architects who are involved in the multi-disciplinary development of accurate motion modules/systems in which thermal aspects play an important role in the overall system performance.
Prerequisites: Technical education (BSc or higher), with at least two years of experience and preferably completion of the course "Mechatronics system design" (Metron Part 1), the former Philips-CTT course Metron or equivalent basic knowledge. Basic knowledge of matrix calculus is recommended but not essential.
The course attracts participants from both the Netherlands and abroad, creating an international atmosphere that fosters valuable knowledge exchange. If you're traveling from outside the country, you can find useful travel information here.
Program
Day 1
- Basics: Thermal System Theory: Common Heat Source in Mechatronic systems; Heat transfer mechanisms; Thermally induced deformations; Transient effects.
- Basic Modelling: Lumped mass modelling; Tooling; Electrical analogy; Hands-on exercise.
Day 2
- Temperature Measuring / Thermal Experiments: Precise thermal measurement techniques; Sensors; Do's & don'ts.
- Case Cryogenic Application: Lumped mass modeling; Simulation.
- Design for Thermal Stability: Main objectives and design considerations for precision equipment; Thermal centre, thermal cancelling & shielding (low-pass, reduction of gradients); Case: applying shielding.
Day 3
- Active Thermal Control: Frequency-thinking for thermal systems; Thermal feedback control design; Bandwidth estimation design rule; Prediction performance of module under control (optional).
- Advanced Topics: Model reduction; Thermal modes; Thermal compensation & sensor placement.
Certification
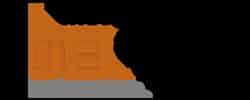

More information
Remarks from participants