This course is certified by the European society for precision engineering & nanotechnology (euspen) and the Dutch Society for Precision Engineering (DSPE) and leads to the ECP2-certificate.
Life without motion is unimaginable. This statement is also valid in the production industry.
Electro-mechanic actuators, driven by highly efficient and accurate power electronic circuits, are the working horses within the industry. They determine the performance and quality of many industrial processes. In high-end industrial applications the accuracy of the production systems is increasing steadily, enabled by ever more powerful, precise, efficient and cost-effective actuation systems.
Several questions can be asked about dynamic mechanical systems that are related with the actuation;
- How can mechanical systems be kept silent (free of motion) in a vibrating environment when large objects are actuated with high accelerations?
- How is a low energy consumption level accomplished when having a frequently alternating load?
- Why are permanent magnets so important for mechatronic drives?
- Is it possible to make strong actuators without permanent magnets?
- How can an electric car achieve such a high overall efficiency?
- What is the role of power electronics in the application of electromagnetic actuators?
These and many other questions will be elaborated in the course. For that reason the fundamentals of electromagnetic actuators and motors including the necessary power electronics to control them will be covered. Detailed attention is given to the challenging task of choosing the right actuator type for a certain application from an overwhelming diversity. The impact of different principles of electronic power conversion will be unraveled, ranging from linear to switched mode power circuits, each with their own benefits and drawbacks. The need for current or voltage drive is elaborated while attention is given for power amplifier noise. Especially aspects of element selection and/or development for short stroke or long stroke high precision linear actuation will be treated and special multi-DOF actuators will be presented as challenging examples.
This training is available for open enrollment as well as for in-company sessions.
Objective
After the course, the participants will be able to initiate, specify, guide the development of a special motor or select the proper off-the-shelf actuator (type & version). Participants will acquire a mix of theoretical background, do's and don'ts and practical insight that is useful when designing mechatronic systems with different actuation systems.
Target audience
This course is intended for mechatronic system designers and architects who are involved in the multi-disciplinary development of motion devices and need a better insight into the various aspects of actuation systems in order to make an adequate selection of available off-the-shelf components or initiate, specify and guide the development of a customized actuation system.
Prerequisities:
University level education, with at least two years experience and completion of the courses Mechatronics System Design (Metron part 1 and/or part 2) or equivalent.
The course attracts participants from both the Netherlands and abroad, creating an international atmosphere that fosters valuable knowledge exchange. If you're traveling from outside the country, you can find useful travel information here.
Program
Day 1
- Introduction & Overview: Learning goals. The role of electromechanical drives in mechatronic positioning systems. Some application examples as preview of the course subjects with a little recap of METRON part 1 and part 2.
- 'Working with' Electricity and Magnetism: Maxwell Equations and Lorentz Force. Ohm’s and Hopkinson’s law: Electric and magnetic modeling with “circuits” consisting of sources, resistances/reluctances, permanent magnets and ferromagnetic parts.
- Power electronics for actuation: Basic analogue power electronics. Semiconductors, Switching diodes, Power transistors and MOSFETS, Linear and Switching electric power conversion. Energy flow in two directions.
Day 2
- Electromagnetic actuators and electromotors: Recap Day1. Basic terms and properties of electromotors and actuators, efficiency, thermal dissipation, performance figures of merit.
- Lorentz actuators and related electronics: Flux linkage vs Lorentz law. Force vs position dependency, current density, dynamic stiffness, damping, current control. Multi DOF actuation. Electrical properties, impact of actuator self-inductance. Amplifier - actuator matching, jerk and snap. Design issues with current amplifiers. Current noise.
- Reluctance actuators and related electronics: Non-linear force, magnetic energy, force of magnetic field, linearization by balancing and feedback. Flux control, permanent magnet biasing, Fast Tool actuator, Magnetic Bearings.
Day 3
- Examples of real motors and actuators: Recap Day 2. Mechanical and electronic commutation. Standard rotating motors. Practical issues. Amplifier-actuator interaction demonstrated on real hardware. Drive control in the first successful hybrid car (Toyota): A useful side effect of current control.
- Recent drive system developments: Commutated systems, long stroke actuators, phi-z actuator, planar motor concepts, parasitic phenomena (cogging and end effects), wireless energy transfer.
- Wrap-up and closure: Language: Dutch or English (depending on the participants).
Certification
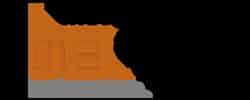

Remarks from participants